CASE STUDY
Materials Tracking
LNG DEVELOPMENT PROJECT
Background
In the last decade, an enormous gas and condensate field in was discovered 220 kilometres off the shore of Western Australia. Subsequently, one of the world’s most complex LNG development projects was initiated, including the construction of the longest subsea gas export pipeline in the southern hemisphere. With a value of approximately $AU63 Billion, it is one of the largest Liquefied Natural Gas (LNG) developments to ever be undertaken.
A reputable EPC/M contractor, was engaged on the project to fulfil a series of objectives, namely:
Results
- ‘Materials’ were no longer used as an excuse for delays to the project.
- Over 76,000 unique line items were created in a two year period.
- Mobile devices were used to process over 135,000 transactions.
- All major users were trained on the new materials tracking solution in just two days.
- 1.4 million items were delivered to the work front with clear documentation.
- The requests of over 1,300 engineers were recorded and managed in one system.
- The Materials Team were able to identify and process materials without delay. The team was also able to prepare test packs to be on the work front before they were requested.
- Reporting features empowered the Materials Team to provide accurate and accountable information.
- The system created an audit trail that held people accountable. It also covered legal obligations regarding chain of custody.
- The system identifed shortages that allowed the team to make data-driven decisions to resolve the issues.
“The biggest problem with materials – especially on large scale construction projects – is finding them and tracking their condition in one system.”
Construction Services Manager
The Challenge
Upon arrival on site the contractor immediately identified a lack of accurate information relating to construction materials. Data mismatches existed between materials in current work packs, laydown yard inventories, and materials still with fabricators.
Information surrounding material handling was stored and processed using bloated spreadsheets. These were full of inconsistent data, and included thousands of line items. It was clear that by the time these spreadsheets were updated and shared with construction teams, the data was already outdated.
There was a need to quickly take control of materials management, stocktakes and inventory levels. Materials that jeopardised workpack or testpack completion needed to be identified long before due completion dates.
It was clear that an improved tracking solution was required to provide continuous visibility on all construction materials, their status and availability. Additionally, this system needed to mould around pre-existing procedures, plugging gaps in the process. With a labour force approaching capacity, fast implementation was required without generating unnecessary extra work.
“Track’em finally gave everyone a reliable view on the status of all materials.”
Technical Services Manager
The Solution
The EPC/M contractor engaged Track’em to roll out their software and assist with uploading the gathered materials status data into the Track’em system and resolve the information gap around construction materials.
The contractor established a team to assess the situation, label all the materials using barcodes, and scan everything in order to gain an accurate picture of the overall status with Track’em’s support. They then uploaded and updated historical data from legacy spreadsheets into Track’em’s cloud platform providing a single source of truth.
Once all the information was digitised and in one place, users were trained on Track’em’s Materials Tracking solution. This enabled them to take control of materials handling and streamline processes.
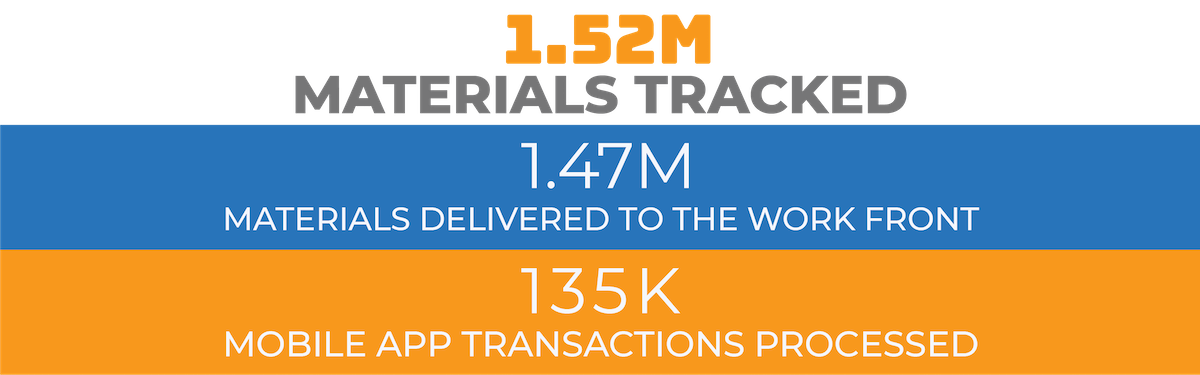
Barcodes acted as the primary source of verified data. Anyone handling materials simply scanned the associated labels, using either barcode scanners or the Track’em app. After scanning the label, staff could change details relating to location, status and custodian. In addition, the process allowed for the addition of supplementary information (such as photographs of damaged components).
The system kept track of all historical transactions. This created a full audit trail for compliance and for use in the event of discrepancies. This audit trail provided full visibility of the chain of custody once materials were in the contractors’ hands.
Different users were given varying levels of system access, based on their individual role and level of engagement with materials. These user-based restrictions enforced gate systems, ensuring data remained clear and accurate.