Built for your organisation
Undoubtedly proven in the construction and maintenance of complex infrastructure in remote areas.
Track'em provides the reliability, flexibility and support needed to get challenging work done on time and budget.
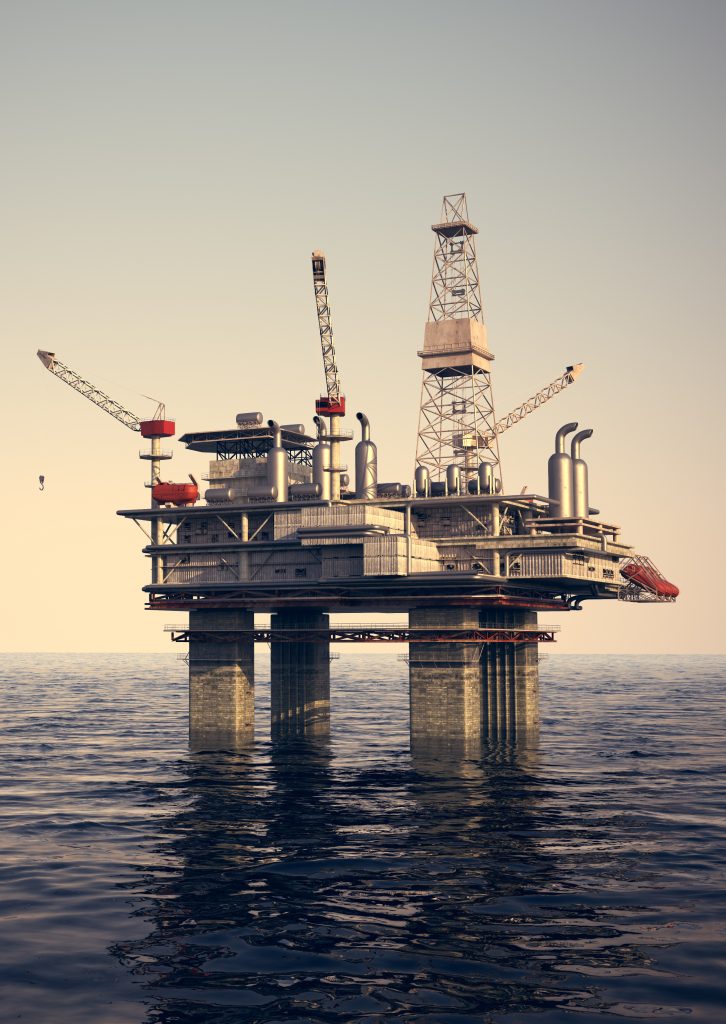
OWNER OPERATORS
LEVERAGE INSIGHTS
Track'em build insights that optimize contractor management, workforce efficiency and project schedules.
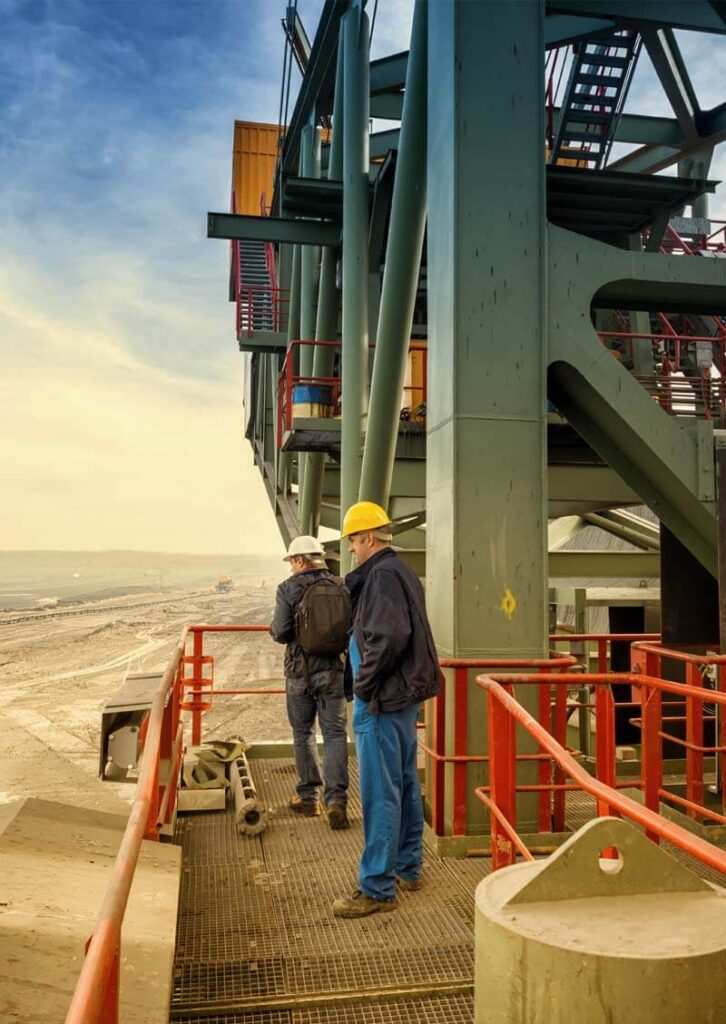
EPC/M and Head Contractors
BUILD YOU REPUTATION
Use the visibility of resources that Track'em provides to achieve a reputation for being in control, driving efficiency and achieving schedules.
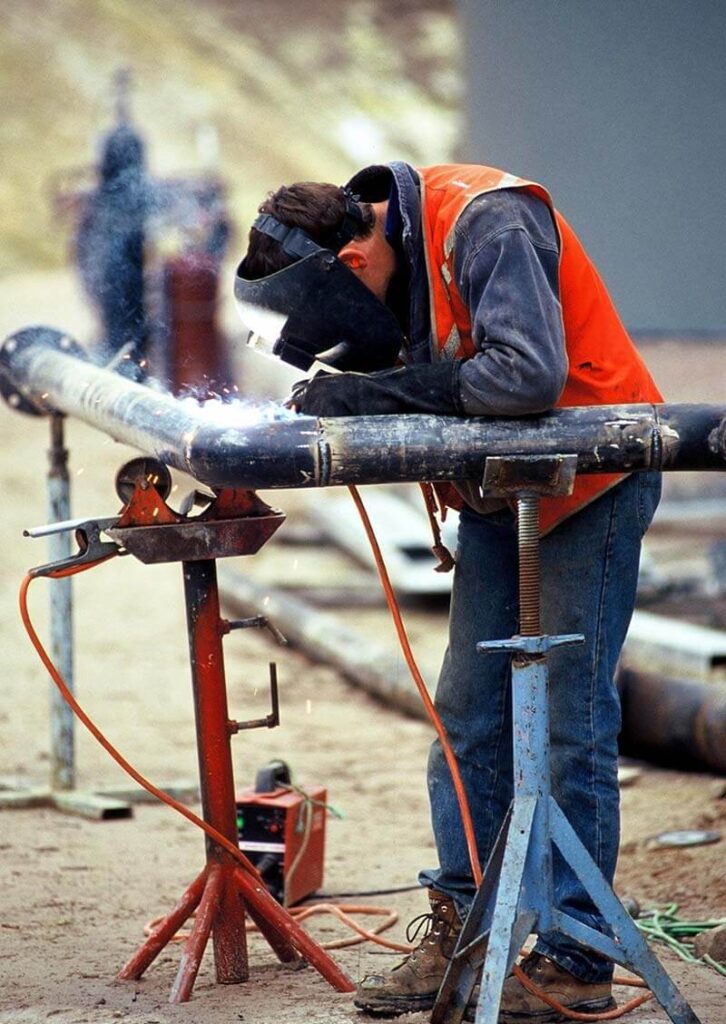
CONTRACTORS
GET PAID ON TIME
Track'em will also support your claims and avoid delays to get paid on time.
Over 10 millions items tracked and more than 50 implementations
Our valued clients
Our ease of use, rapid deployment, fast payback, industry specific functionality and flexible local support has made us a platform of choice for many of Australia's leading construction, engineering and resource companies who have depended on us to track over 10 million items across 50 major projects.
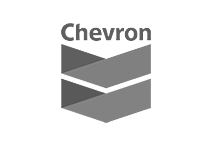
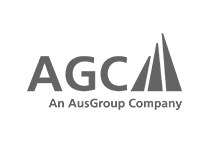
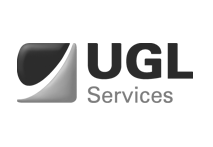
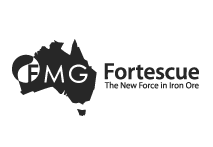
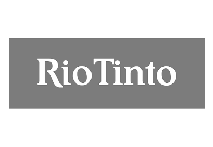
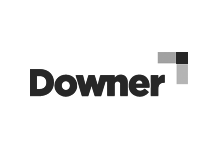
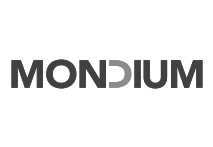
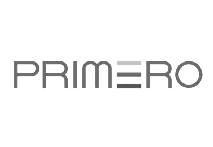
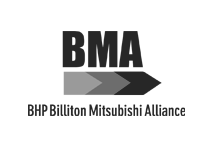
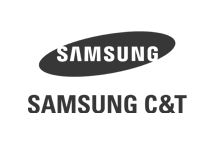
Why choose Track'em?
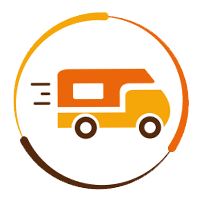
Rapid Deployment
Rapid to deploy, easy to use
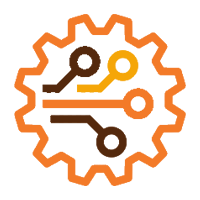
Broad Integration
Integrates with multiple tracking technologies and business systems
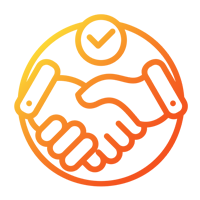
local support
Responsive and ongoing support
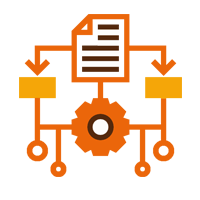
industry optimized
Optimized for construction, engineering, mining, oil and gas
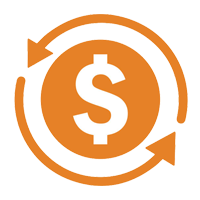
Fast Pay Back
Fast pay back period following implementation
Feature Case Studies
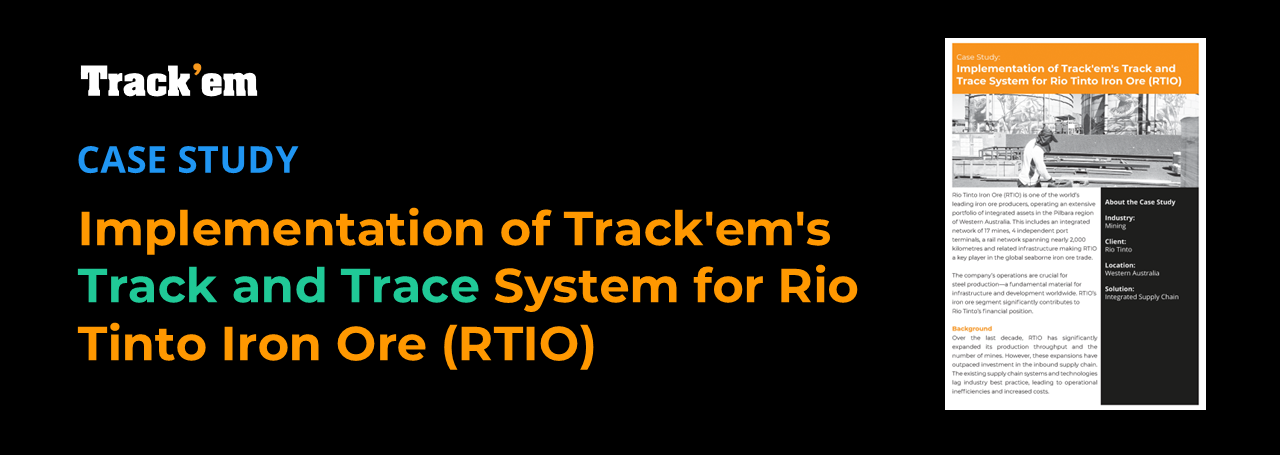
Case Study: Rio Tinto Iron Ore
Customer Type: Owner Operator
Product: Supply Chain Tracking, SAP integration, 3PL Integration
Track'em worked with Rio Tinto Iron Ore to modernise its inbound supply chain, integrating a Track and Trace system across 17 mines, ports, and logistics hubs.
By addressing key gaps—such as poor visibility, system fragmentation, and costly delays—the solution reduced maintenance disruptions, avoided unnecessary freight, and improved warehouse-labour coordination. Live integration with SAP and real-time tracking now allows teams to see exactly where critical parts are, improving planning, reducing downtime, and supporting safer, more efficient operations.
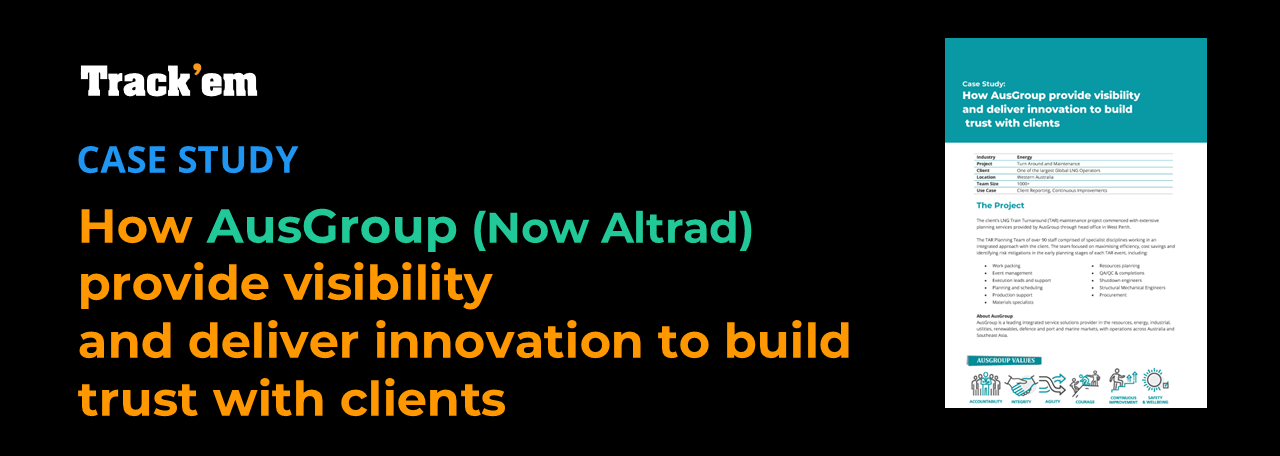
Case Study: AusGroup (now Altrad)
Customer Type: EPC
Product: Time Tracking, Progress Tracking, Payroll Integration, Estimation, Rostering
AusGroup partnered with Track'em to digitise time tracking during a major LNG maintenance turnaround. The solution eliminated manual timesheets, streamlined approvals, and gave supervisors tools to track hours, manage work orders, and report variations in real time.
Within the first month, over 5,000 hours were saved—including 775 supervisor hours—boosting productivity, improving payroll accuracy, and enabling better project forecasting through data-driven insights.
Whitepapers
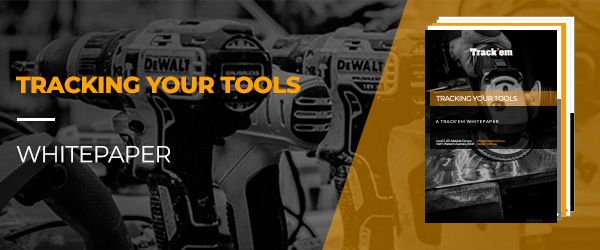
Download the whitepaper and understand the benefits, possibilities and limitations when it comes to tracking your tools.
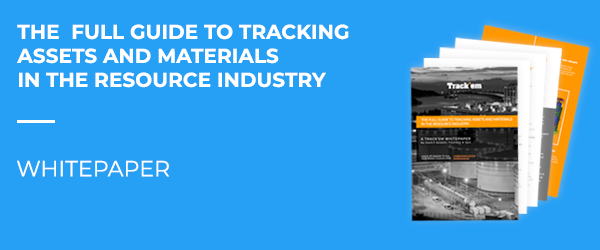
Download the whitepaper and learn how to track assets, materials, tools, plant and equipment, consumables.